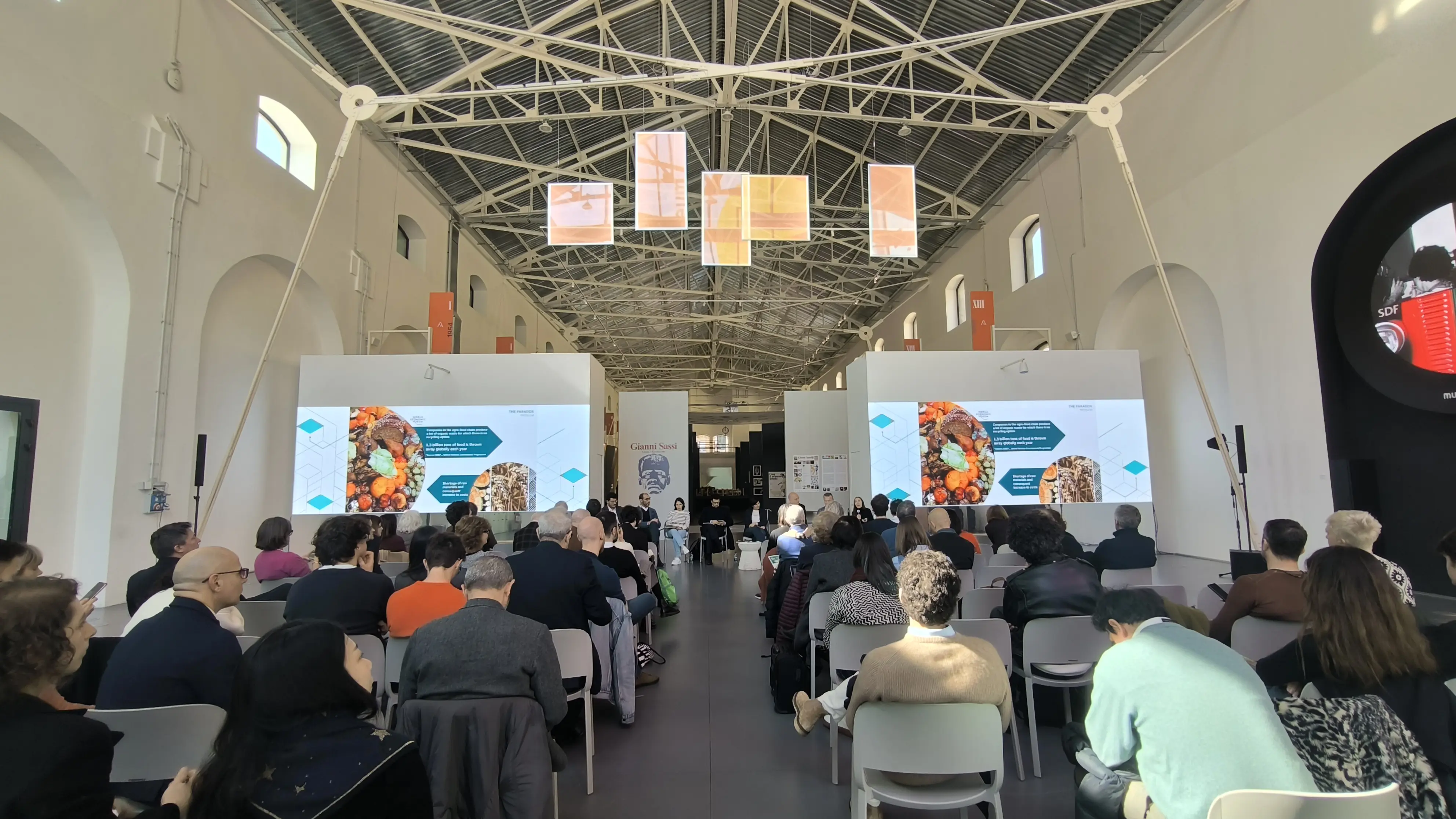
The Scale of Commitment – Incipit
On March 4, the ADI Design Museum hosted the first event in a series of meetings
and exhibitions curated by Materially for Milan Design Week 2025. This event served
as a preview of the April initiatives, focusing on the measurement of environmental
impact and the performance of materials. Below are the key takeaways from the
morning, moderated by Emanuele Bompan, director of Materia Rinnovabile.
Omar Degoli, Head of Environment and Circular Economy at FederlegnoArredo,
addressed the challenge of transferring the success of the Ecodesign regulation for
electronic products into the new ESPR (Ecodesign for Sustainable Products
Regulation). This regulation, which is currently being defined, will cover five sectors,
including textiles, furniture, and steel.
Several options are under consideration by the European Commission. One option
involves environmental protocols or minimum environmental criteria—sets of non-
scientific guidelines that address significant issues within specific product categories,
such as furniture. Another approach is measuring the actual characteristics of
products, like carbon footprints, to be included in Environmental Product
Declarations (EPDs). While this approach has worked for electronic products, it may
not be suitable for quality-focused industries like Italian furniture production, which
can be less scientifically standardized.
FederlegnoArredo advocates for a system based on technical product standards, a
pre-existing corpus of guidelines that could be made more binding. These standards
aim to extend product lifecycles and reduce waste, while promoting sustainability
without imposing additional burdens on the industry. One of the most innovative
aspects of the ESPR is addressing obsolescence.
Sara Corrado, Group LCA Lead at Broadview’s Center of Excellence for Innovation
and Technology, highlighted how Life Cycle Assessment (LCA) has become an
essential tool for evaluating products within the company’s global portfolio, which
includes well-known laminate and coating brands like Formica and Fenix.
Broadview’s sustainability efforts began in 2010 with outsourced LCA studies, and in
2017, the company established a dedicated sustainability department that has since
expanded to thirteen people.
LCA was initially used for internal purposes, such as quantifying impacts across the
production cycle. More recently, Broadview has expanded its LCA efforts to product-
level communication through EPDs, which go beyond carbon footprint measurement.
The company also follows an EPD Process Certification, ensuring that its LCA
system is reliable and transparent. The lack of unified criteria for secondary data is a
significant challenge, particularly regarding energy consumption, which is calculated
differently across reference databases. Broadview welcomes the development of a
European-level database to address this issue.
Lamberto Lamberti, Head of Sustainability at the Lamberti Group, discussed how
measurement is intrinsic to the company’s business. Lamberti develops innovative
ingredients for various sectors, including energy, agriculture, surface treatment,
ceramics, personal care, and natural polymers. Their scientific approach to
measurement drives improvements in product performance and sustainability.
Over the last decade, Lamberti has focused on new applications for materials,
including lighter, more resistant, and more sustainable options. The company has
continued to invest in research and development, including sustainability parameters
that are increasingly requested by their customers.
Serena Gazzo, Sustainability Data Analysis Manager at Lamberti, explained how the
company formed a dedicated internal team for Life Cycle Assessment between 2020
and 2021. The team, consisting of specialists in regulatory certifications,
communication, and chemical R&D, helps Lamberti meet eco-design goals by
optimizing environmental performance at the R&D stage.
As demand for LCA services has grown—Lamberti has handled 150 requests in the
last three years—they are developing a digital platform to streamline the process and
update both primary and secondary data efficiently. The organization Green
Chemistry for Sustainability is also creating a shared database for the chemical
sector, which will help increase transparency and data-sharing.
Marco Pelucchi, President of AIPEF (Italian Flexible Expanded Polyurethane
Association), discussed how polyurethane faces challenges due to “chemophobia”—
a lack of understanding about its production processes. He emphasized that
polyurethane production does not involve harmful chemical discharges and has
undergone extensive research to make it more eco-friendly.
Over the last two decades, solutions have been developed to address the large
amounts of waste and by-products generated during production and cutting.
Mechanical recycling, which involves shredding polyurethane, is effective for creating
high-density agglomerates. However, this method is unsuitable for post-consumer
polyurethane waste, which is contaminated both biologically and chemically.
Chemical recycling, carried out upstream in the supply chain, can transform waste
into polyols, though these polyols currently face performance and cost limitations. A
third recycling option is waste-to-energy.
Pelucchi advocated for single-material furniture designs, which can improve the
circularity of products. For example, polyurethane of appropriate lift could replace
wooden frames in upholstered furniture, ensuring more efficient end-of-life
management. Additionally, reducing the size of polyurethane during transport
through vacuum sealing is a significant step toward improving the material’s
environmental performance.
Martina Lamperti, Founder of Krill Design, discussed the challenges that small
players face in assessing environmental impact. Krill Design is an innovative start-up
focused on solving two key problems: the vast amounts of organic waste generated
annually by food and beverage companies and the scarcity of raw materials. The
solution Krill Design offers is a new secondary raw material created from organic by-
products. This material, called Krill, is biodegradable and compostable, and it is used
to create products for the same companies that produce the waste.
Originally made from orange by-products, Krill now includes a diverse range of
materials with technical characteristics similar to traditional plastic, but with a more
natural appearance and feel. However, scientific validation of Krill’s environmental
benefits came through a collaboration with Milan Polytechnic. A PhD student
conducted a cradle-to-gate impact analysis, measuring the equivalent CO2
emissions (excluding the use phase). As more customers demand certifications and
LCAs, Krill faces challenges in obtaining timely and reliable data for a new material
like theirs.
Andrea Mulloni, Head of Sustainability at Arper, discussed the company’s long-
standing commitment to sustainability. Since 2005, Arper has focused on creating
low-environmental-impact products. Initially, LCA was used mostly as a compliance
tool, but three years ago, Arper shifted its approach to set sustainability goals from
the design phase, which accounts for 80% of a product’s environmental impact. This
change led to the creation of a Sustainability Office, independent of Quality Control,
and the development of products like Catifa Carta.
Catifa Carta is a chair made from twenty-nine layers of craft paper bonded by a bio-
based binder derived from linen hemicellulose, making it 100% biogenic while
offering performance similar to traditional plywood. The project also focuses on end-
of-life solutions, as most furniture returns its CO2 content to the atmosphere when it
decomposes. With Catifa Carta, Arper and its partners developed a circular model,
collecting disused chairs and transforming them into biochar through pyrolysis. This
process prevents CO2 emissions and creates a material that can be used in
construction, industry, and agriculture.